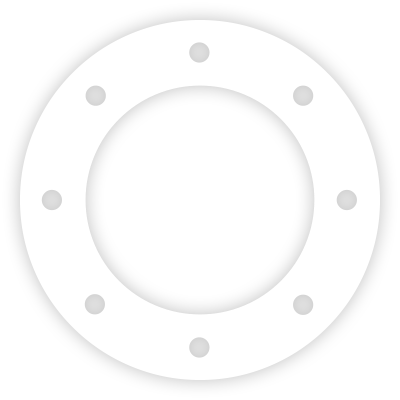
0%
为什么清洁技术应该由特定的应用程序来确定,而不是由现有的系统技术
无论是在汽车、航空和航天工业或者工程领域:在世界各地成品的质量被认为是研发和高端制造、创新工业产品的标签。很显然,即使在部件的最小污染都意味着是在随后的制造工艺中的“齿轮中的沙子”。
工业清洗技术被用于可靠地去除从大的到微观小的污染物,。然而,在为一个新的系统的工程的要求选择供应商时考虑并不总是很周到。或者,项目范围实际上是适应于一个现有的、但有局限性的系统的性能特征。这导致以实现其以质量、运营成本、产量和灵活性的性能要求方面只有微小的效能或完全失败。
但是也有不同。我们在里德里西的LPW 清洗系统有限公司的人士认为,机器和清洁方案的设计应满足客户的个性化应用,而不是现有系统技术的可行性。
„合格的可行性测试省事又省钱。“
要求规范是针对零件的清洁度、产能和后续工艺的要求制定任务的基本依据。
实际的清洗任务是由其必要的清洗工艺要求结合下述因素来确定的:
项目的讨论也包括
使用合适的示范系统进行可行性测试和清洗试验可以被用于可靠地确定适当的清洁工艺。
当高产能比工件的清洁度更重要的时候,解决的办法通常是开放的,多液槽形式的中央清洗系统。
优点: 高产能(15〜20 盘/小时,根据要求)
缺点: 较低的过滤能力、使用机械清洗选项的限制,如洪水总量和泵的压力以及由增加的维护、由于开放式液槽导致的高于平均水平的能耗等所导致的高运营成本,处理不同材料的能力和/或同时进行不同的清洗任务的限制。
较低的产能,但具有:
不过模块化腔体技术,即提供了广泛的产能和灵活性方面的能力,同时也保留了单腔技术的知名优势。
系统的技术设计准则不应只针对所期望的清洁结果和产能,也要考虑经济因素,如初始投资、直接和间接的运作成本和整体系统的可用性。此外,设备利用率波动中单件成本的变化也起着重要的角色。模块化系统非常理想地把所有这些标准纳入了“总包”。
„清洗系统必须适应客户的要求。而不是反之。“
生产设备和系统的适应性是工业清洗技术成功的关键。下面是关键因素:
由LPW清洗系统公司开发和制造的模块化系统技术,提供了范围广泛的相关选项,可以量身定制以成为现有流程中不可或缺的一部分。这也适用于简单的中间清洗(例如脱脂,排屑和干燥),以及对微粒和润滑剂膜复杂的最后清洗。
![]() |
标准工艺腔体的设计用于大多数应用(舍费尔篮筐1和2以及超大尺寸),适合于任何类型的清洗和干燥工艺。 |
![]() |
带介质流通和液位监测系统的储槽系统。为电加热,燃气加热或外部热源而设计。 |
![]() ![]() |
适应于所有常见的干燥工艺。 |
![]() ![]() |
各种功率和频率范围的超声波,2〜100立方米/小时的泵容量和压力范围为2至20巴。 |
![]() ![]() |
特定任务的全流量或旁路介质处理系统。 |
![]() |
为更苛刻的清洗任务的超精细清洗组件的综合能力。 |
![]() |
配置上采用了介质存储和工艺腔模块可任意组合,以及扩大选项。升级选项。 |
![]() |
标准化的自动化/上料的解决方案,可适于所有配置选项,无显著的额外费用。 |
自动化是上游和下游工艺之间的链接。以满足当前和未来任务的各个方面,必须即稳健又安全。
自动化清洗设备必须具备以下特征:
对于简单规格的典型滚筒输送机具有客户定义的负载站可能就足够了。对于这些类型,模块化,标准化是很容易实现的,即使有不同的特点和负载范围。
对于要求更高的任务,如具有多个装载台的多级清洗工艺中,常规类型的使用大量的单个部件(逆变器,装载系统,分离器等),并且可以涉及很复杂的技术。
添加额外的要求,如分离已清洗/没清洗产品或在同一系统上对同一批货的中间清洗和最终清洗,传统的解决方案迅速达到它们的极限。技术风险增加,并最终影响整个系统的可用性。
这方面的一个变体是LPW穿梭运输和装卸系统,它具有一个水平长轴,在其上的装/卸穿梭具有分别的清洁和脏物位置来处理所有传送和装卸工作。
它大部分可以省掉篮筐的停止,也允许可靠的交叉横向运输。穿梭是模块化的,可以很容易地以低成本适用于当前和未来的项目要求。
„一切皆有可能。“
应用举例:铝压铸件,无毛刺,最大粒度200-300微米。我需要做什么?什么是正确的清洗技术?
„模块化设计提供了更大的灵活性和更好的性能。“
产业 | 汽车/乘用车燃料喷射系统 |
---|---|
任务 | 清洗,超细清洗,冲洗和自动冷却到洁净室组装 |
工件 | 各种加工后的钢/不锈钢工件 |
批量大小 | 670×480×300毫米 |
批量重量 | 最大 150公斤 |
产量 | 10-14批/小时 |
要求 | 无碎屑,磷酸盐层,干燥 |
将主清洗和冲洗分离可以提供一个几乎完全没有污染的完整工艺。此外,分离工艺所降低的循环时间可被用于附加的工艺步骤。
![]() |
2工艺腔体 |
![]() |
腔体带1个清洗槽/1个漂洗槽 腔体2带1个漂洗槽 |
![]() |
腔体1,喷射/压力洪水 |
![]() |
腔体1,超声波10瓦/升 |
![]() |
所有液槽全流过滤 |
![]() |
腔体1,中间干燥 腔体2,热空气干燥 |
![]() |
腔体2,真空干燥 |
![]() |
D蒸馏系统 聚结分离器油 |
![]() |
没有集成精密清洗 |
![]() |
带传统的辊道输送机的自动化连接到洁净室 |
![]() |
洁净室之前的冷却隧道 |
标准化程度:95%
产业 | 一般工业/液压 |
---|---|
任务 | 清洗,漂洗,长期保存 |
工件 | 车加工后的钢零件 |
批量大小 | 670×480×300毫米 |
批量重量 | 150-200公斤 |
产量 | 10-14批/小时 |
要求 | 颗粒大小,干燥,长期保存 |
![]() |
2个腔体 |
![]() |
腔体1 带1个清洗槽/1个漂洗槽 腔体2带一个防腐槽 |
![]() |
无机械清洗 |
![]() |
腔体1,超声10瓦/升 |
![]() |
所有液槽全流过滤 |
![]() |
腔体1,中间干燥 腔体2,热空气干燥 |
![]() |
腔体2,真空干燥带冷凝水收集 |
![]() |
油聚结器 |
![]() |
没有集成精密清洗 |
![]() |
带传统辊式输送机的自动化 |
![]() |
腔体1和腔体2的真空填充 |
这个系统是为具有喷淋能力的清洁介质和矿物油基的防腐剂而设计的。真空填充工艺使得能够使用这两种介质。双室设计还保护腔体1的清洗槽的附加油的带入,从而减少清洁剂消耗。真空防腐工艺中也确保油膜被均匀地施加在所有的表面上。
标准化程度:80%
产业 | 一般工业/汽车行业 |
---|---|
任务 | 清洗/热能式去毛刺之后的防腐 |
工件 | 钢/铸铁 |
批量大小 | 670×480x400毫米 |
批量重量 | 200 公斤 |
产量 | 7-8批/小时 |
需求A | 无氧化,短期/长期保存,干燥 |
要求B | 第二个双腔系统扩展能力 |
本要求C | 能够处理单批次 |
![]() |
2个工艺腔体 |
![]() |
腔体1带1个清洗槽/1个漂洗槽 腔体2带2个漂洗槽 |
![]() |
腔体1,喷射/压力洪水 |
![]() |
腔体1,超声波 |
![]() |
所有液槽全流过滤 |
![]() |
腔体1,中间干燥 腔体2,热空气干燥 |
![]() |
腔体2,真空干燥 |
![]() |
油聚结器 |
![]() |
没有集成精密清洗 |
![]() |
带穿梭机的自动化连接到1个装载回路,1个卸载回路以及溶剂清洗/保存; 为另外的2腔型清洗系统制备 |
![]() |
RFID系统,连接到生产控制中心 |
标准化程度:80%
„为明天的工作规划。“
产业 | 汽车行业/喷射系统 |
---|---|
工件 | 中央的中间和最后的清洗 |
工件 | 钢/不锈钢工件 |
批量大小 | 670×480×300毫米 |
批量重量 | 200 公斤 |
产量 | 6-12 批/小时 产量:6 – 12批/小时,根据任务(每年500万的钢工件,约13,000 - 14,000批。每年3000万的不锈钢零件,约25,000 - 26,000批。) |
要求 |
工件1: 钢的加工和磷化后的最终清洗。目的:粒度<250微米,立体,至少6个月的防腐保护。 工件2: 不锈钢加工和毛刷工艺后的最终清洗。目的:粒度<200微米,无痕迹。 |
附加要求 | 预清洗/中间清洗及最终清洗并用一个系统的工艺,非结构化批量处理包括单批次,对所有工件在所有程序中的清洗和第一漂洗,对不锈钢工件的独立高流动的纯净水漂洗,对不锈钢材工件的单机干燥及钢工件的防腐清洗 |
![]() |
6个工艺腔体 |
![]() |
5个液槽(清洗,漂洗1 - 3,防腐) |
![]() |
腔体1,喷射/压力洪水 在回路1,3和5中的频率控制的泵 |
![]() |
腔体1中,超声波10瓦/升 |
![]() |
在所有液槽全流过滤 |
![]() |
腔体1,2,3和4中,中间干燥 腔体5和6中,热空气干燥 |
![]() |
腔体5和6中,真空干燥 |
![]() |
油聚结器,蒸馏系统 |
![]() |
腔体4带超细清洗模块 |
![]() |
穿梭机自动化与1个装载/卸载回路连接 |
![]() |
RFID系统 |
标准化程度:100%
应用实例表明,无论什么工艺和能力要求,基于模块化配置的定制系统提供了即为大规模集中也为规模较小的分散任务的解决方案。
这种复杂的模块化提供了配置了各种各样系统的能力,以满足当前和未来的生产要求。有限的复杂性和巨大的灵活性优化这些系统的运行成本和减少技术风险。
更多的信息您可以在这里下载我们的中文产品说明书:
→ LPW产品说明书下载
点击这里了解更多信息:
www.lpw-reinigungssysteme.de
或直接与我们联系:
info at lpw-reinigungssysteme dot de